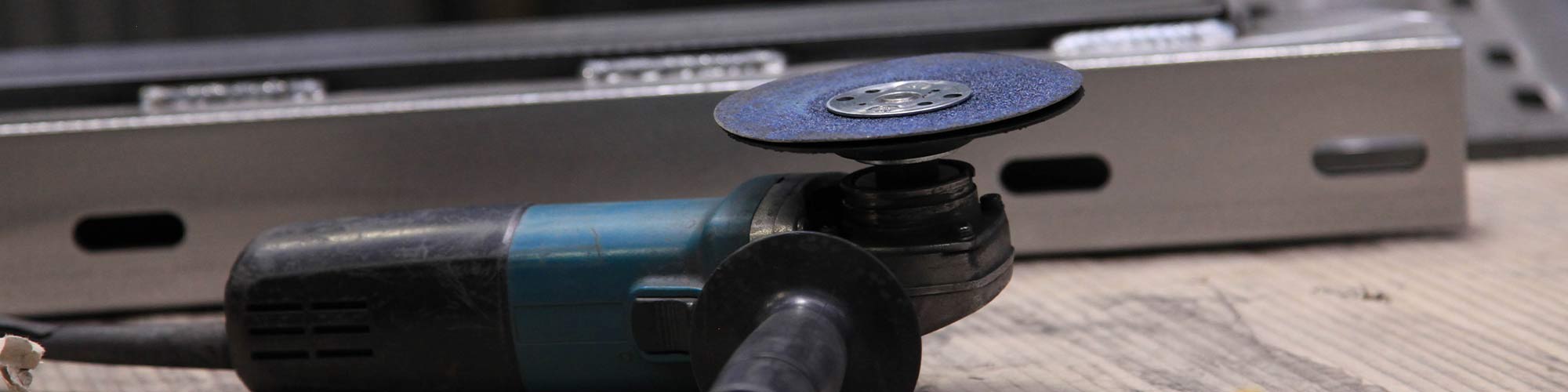
Our History
Shermaynes Engineering Limited was founded in the North West of England in 1960 and currently employs over 35 members of staff in and our 38,000sqft factory. Our established business continues to provide a complete and exceptional metal working service for its customers today to the highest of standards.
1960 - Beginnings
Starting from a small unit on the Morecambe industrial estate where we still operate, Shermaynes (Welders & Engineers) Limited was incorporated in 1960. Early work for the business included the fabrication of concrete mixers, various storage equipment, and mobile trollies.
1976 – Sheet Metal
To meet the increasing demand for sheet metal components, a second factory was opened which focused on precision sheet metal work, including stainless steel.
1980 – Powder Coating
Having previously offered Stove Enamelling, we switched to Powder Coating which significantly improved throughput and product quality, in a much wider range of colours and finishes.
1985 – CNC Punching
Our first CNC punching machine, and one of the first Amada CNC punch presses in the UK, was installed in order to vastly expand our profiling capability and repeatability.
1987 – Consolidation
After years of moving parts between the two shops via road, we moved into our current 38,000 sqft building in January 1987. During one of the coldest winters on record in the UK, in which icebergs were observed on the River Lune, the installation team and subcontractors worked in a freezing cold building to construct the offices and prepare the factory for the equipment to be moved across.
1988 – Additional Punching Capacity
As part of our ongoing expansion, our original Amada punch was replaced with 2 new machines, offering more flexibility. A third machine would be added in 1995.
1996 – A New Chapter
A new company, Shermaynes Engineering Limited, was formed with the same management team to take over the operations of the business from the previous owners.
1997 – ISO9002
As part of our commitment to quality across the business, Shermaynes Engineering Limited was awarded ISO 9002:1994 accreditation in 1997.
2008 – 3D CAD
From the early days of drawing boards and then 2D CAD software, as a subcontractor it’s important to be able to work with whatever format of drawings our customers supply. We added Radan 3D and later SolidWorks 3D, enabling us to take customer 3D models and convert them to flat patterns for our profiling machines, without working with intermediate 2D CAD prints.
2010 – Laser Cutting
While maintaining our extensive CNC punching capacity, we added CNC laser cutting due to increased customer demand and the small-batch flexibility of a laser. Using the same programming system across all of our profiling machines, we are able to send jobs to whichever workstation is best suited.
2014 – Laser Marking / Laser Engraving
An example of how the requirements of our customers drive our investment decisions, a new series of parts requiring laser marking over large areas led to our investment in one of the fastest large format CO2 marking lasers available. This also opened up possibilities in non-metallic production for the first time, with various plastics available to process.
2017 – ISO 9001
After a big change to the ISO standard, our management system was accredited to the new ISO 9001:2015. A constant work-in-progress, we look for opportunities to improve every day.
2022 – ISO 14001
As part of our commitment to controlling and improving the environmental impact of the business, our environmental management system was awarded ISO 14001:2015 accreditation.
2022 – Fibre Laser Cutting
We updated our laser capacity with a new Fibre machine, offering a greater processing range, improved speeds and reduced energy requirements.
2023 – ISO 45001
The next step in our Integrated Management System approach, our Health & Safety management system was awarded ISO45001:2015 accreditation.
2024 – Cobot Welding
In recognition of the changing skills landscape, we invested in our first Cobot welding cell. In conjunction with jig design via 3D CAD, using the model of the final component, we can quickly produce welding jigs for repetition work. This leaves our highly skilled welding operators free to focus on the more challenging jobs that we always thrive on as a subcontractor.
We place importance on service excellence and the levels of quality we strive to uphold
Kind Words
‘It’s all about the people with Shermaynes. They really do go the extra mile for you no matter what’